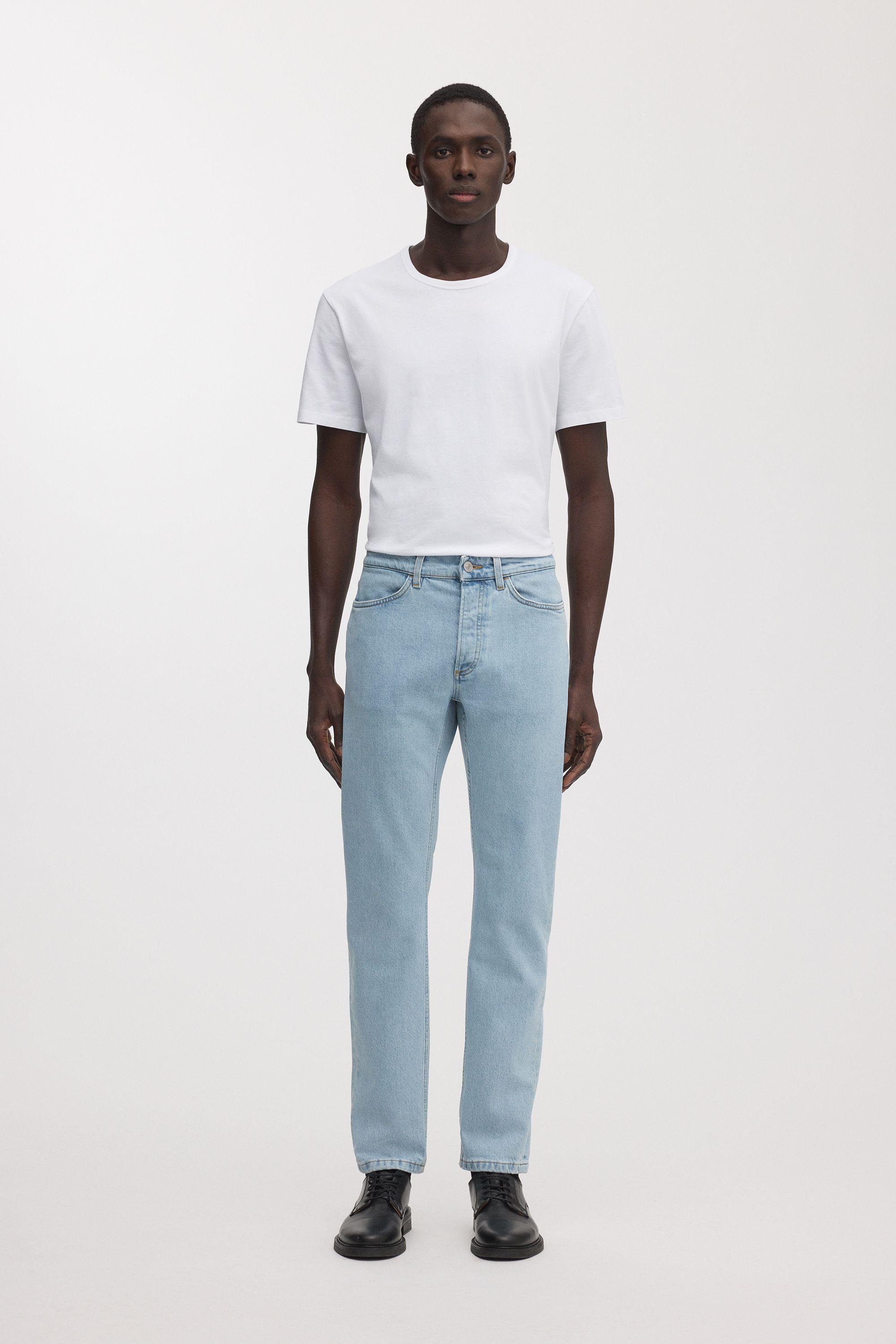
The Slim Jeans
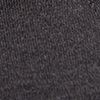
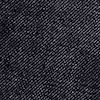
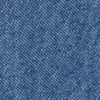
+1
Light Blue Wash
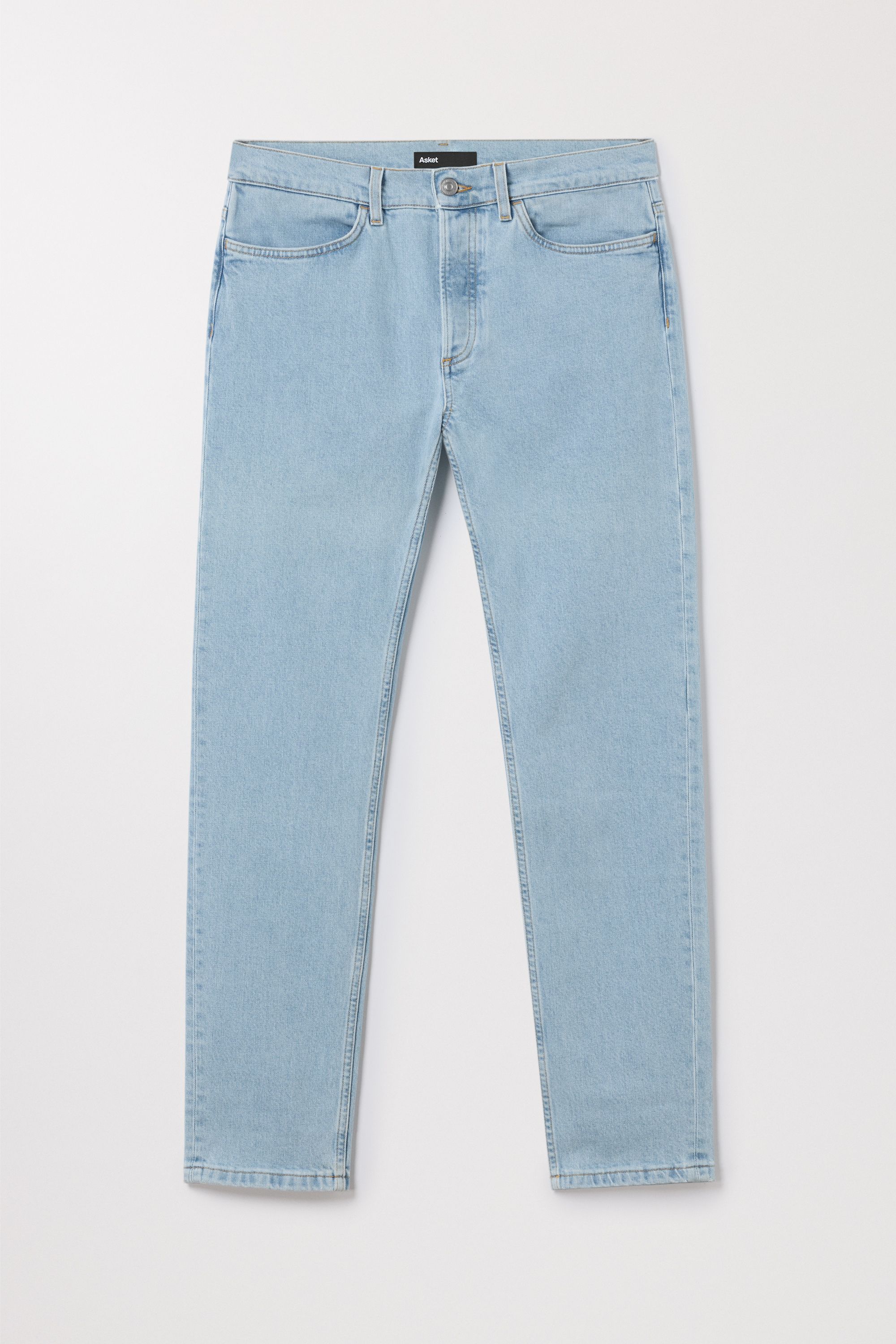
Everything you'll ever need to know about denim - and the Asket denim lineup specifically.
The appeal of Denim is pretty much universal. Most people will have at least one pair of denim jeans and every brand has their own iteration of them. They have a history that stretches back about 400 years and have been used for a high variety of purposes and — today — they are not just a staple of our wardrobes, but undoubtedly the essential pair of pants across all industrialized cultures. It’s no understatement that the introduction of jeans and its subsequent surge in use forever changed male and female fashion.
There is a lot to Denim. More than many of us can even imagine and more than we can ever dream to lay out on a single-page without having you fall asleep on your desk. To make this deep-dive engaging is to achieve depth while at the same time not going all too far beyond its rugged surface. Whether you are a newbie or a true denim head, there is always something new to learn.
The word “Denim” goes all the way back to the 1600s and stems from the French “serge de Nimes”, which means a “sturdy fabric from Nimes”, the place where the first denim fabric ever was produced. The term “Blue jeans” has its origin in Genoa, Italy, where it was worn by manual laborers. The first textile mills already started emerging in America during the 1700s, which were responsible for the first so-called “waist overalls” to be worn by laborers. But, it wasn’t until the gold rush in 1873, when miners required exceptionally durable clothes, when what we today know as “denim jeans” today surged in popularity. It was here where the first pair of rivet-reinforced denim jeans saw the light of day by the hands of an ingenious local tailor local to Nevada called Jacob Davis. He became a close business partner with Levis Strauss, who was able to help him mass-produce denim work jeans. During the late 1800s and early 1900s more manufacturers, including the likes of Lee, Carhartt, and later: Wrangler entered the market due to the high demand for durable work wear in a variety of industries and the “cowboy craze” in the 1930s. During the mid and later 1900s, denim jeans started moving away from its original purpose of being specifically for hard, manual work. It became a cultural symbol for independence and a sartorial statement in a huge variety of political movements and subcultures, from the hippie movement in the 1960s to punk rock in the 1970s and Hip-Hop in the 1990s. In short, denim jeans and the gradually increasing number of variations of them started seeping into everything.
Female welders during WW2
INDIGO DYES
If you are even slightly into jeans, you will probably have heard of the term “indigo”, which comes from the plant called Indigofera Tinctoria. Its widespread availability of the indigo plant (Full name: Indigofera Tinctoria) made it a go-to for dyeing the denim yarns.
To create the dye — which looks like a dark blue powder — the plant has to go through the extensive process of getting soaked, alkalized, oxidized and finally dried. A little fun fact about natural indigo: it has protective properties against microorganisms.
The vast majority of indigo produced today — however — isn’t actually made from the plant; it has been replaced by a synthetic compound introduced in the late 1800s primarily for being significantly more economically viable and easier to deal with. Natural indigo is a whopping 10 times more expensive. There are 2 types of synthetic indigo: powder and liquid. Liquid is the more environmentally friendly method requiring 50% less chemicals but is also significantly more expensive.
THE WEAVE
Denim is a type of twill weave made from cotton. It is produced by two cotton yarns that are woven together. The yarn that runs across the weave (called the weft) runs over and under the yarn that runs downwards, perpendicular to it. The standard structure of twill has 1 weft yarn passed under 2 or more warp yarns until it passes over one warp yarn again. Traditional denim — the indigo colored raw type — has its warp yarn dyed blue, and the weft dyed white and the most common structure is three to one.
THE AGING
All denim will fade and mold itself to the patterns of its wearers sooner or later. How and how fast will largely depend on the weight, the type of weave and of course how it’s used, how much day-to-day friction it’s exposed to and how it’s washed. Because of the white underside of indigo denim, it will gradually whiten in the parts most exposed to abrasion. The gradual aging of denim is probably one of its main selling points; it should be embraced rather than avoided. A denim head will make a science out of it and you shouldn’t be surprised he’d be able to give a story behind every single mark on his cherished pair of jeans.
THE WEIGHT
Denim is always measured in oz (ounce) and most denim typically ranges between 9 and 16. The weight of the garment significantly influences how it will wear, feel and age. Typically, the heavier the fabric the more rigid, warm and durable it is. A lightweight pair wears in significantly faster and is going to be more suitable for warmer climates. A midweight pair around 10 to 13 is considered to capture the best of both worlds and is — as a result — the most versatile.
Rope Dyeing Indigo at our partners in Japan
Denim is unique in its ability to produce a variety of different outcomes; it is arguably the most adaptable fabric that exists today. This can make producing denim an intricate process that involves a variety of stages and a variety of production methods to choose from in every stage, which usually depends on the desired specifications in the end-product. These can include: type of wash and dye, price-point, the inclusion of elastane or not and more. Here’s a short summary on the most popular methods that exist today.
All denim starts with cotton fibers that are drawn out and twisted together to create yarns. This process is called “spinning”. Today, there are two common spinning methods: ring-spinning and rotor-spinning (also called: open-end spinning). In short, the former is more capable of handling and typically used for long fibers, is slower, carries a higher production cost, but produces a stronger and softer yarn. Rotor spinning is up to 5 times faster than ring spinning but yields weaker and coarser yarns.
After the spinning stage, the yarns are transferred from their individual cones to a large warp beam allowing them to be dyed in bulk. The two major yarn dyeing methods used today are rope dyeing and slasher dyeing. Both have their own pros and cons. Rope dyeing is more suitable for traditional indigo denim and produces deeper and more uniform colors, but is less flexible when having to transition colors than slasher dyeing. Both of these methods belong to the process of yarn dyeing.
Certain denim products undergo a piece dyeing phase either completely forgoing yarn dyeing or to add an additional finish to the end product after the yarn has already been dyed. The three most common methods are reactive dyeing, pigment dyeing and direct dyeing with the first being the most expensive but producing the best color fastness.
After the dyeing stage, the dyed ropes of yarn are wound over a beam to create a wide sheet of yarn next to each other, after which the weaving process starts, where the warps are interlaced with the wefts, turning the yarns into the recognizable denim fabric.
Washing is one of the final — but all the more critical — steps in the production of jeans; it will influence both the color and how the surface ends up feeling to the touch.
Rinse, stone, and enzyme washing are 3 of the more common methods, involving either the use of detergents and softeners, enzymes or stones to make the denim fade, soften and to remove certain undesirable characteristics of natural denim and make it overall more pleasurable to wear.
The weaving process at our partners in Japan
Our raw denim is made from 100% organic cotton, weighs 13oz and follows a 3/1 structure. The denim fabric used for our raw denim jeans and jacket has its yarn spun by following a ring spinning process developed in Aichi, Japan, in the 1970s which enables a much desired natural surface. Ring spinning is one of the oldest methods and produces a stronger and softer yarn compared to other processes. The yarns are then dyed at a half-a-century-old denim dyeing house in Fukuyama particularly renowned for their rope dyeing process that enables even better color depths. During rope dyeing, the yarns are twisted into a rope and are continuously dipped and oxidized, which results in the depths of color the best denim is so renowned for. But it isn’t until the finishing process when the true characteristics of quality denim come to life. Here, in what is also known as Japan’s Denim Valley, lies the secret ingredient to what separates good from exceptional denim. We weren’t allowed to reveal much on their methods, but rest assured that every centimeter of the fabric undergoes meticulous scrutiny, from spot checking to controlling for shrinkage and stability. Our raw denim is “sanforized” which means that the denim is stretched, shrunk and fixed to minimize shrinkage during washes in the eventual use phase and to ensure a perfect fit. After the fabric is finished, it’s sent to the cutting factory in the mountainous Urbania, Italy that has over 50 years of experience in a field that remains highly specialized. The panels are then sent to a family-owned sewing facility in Monsampolo Del Tronto, Italy carrying over 35 years of experience and delivers to some of the highest-end clothing brands in the world.
Our washed, blue denim in Regular and Loose Fit are made from 100% organic cotton, have a weight of 13oz and follows a 3/1 structure. The Slim Fit are made from a slightly lighter 12 1/4oz organic cotton denim with 1,5% degradable elastane for more freedom of movement. The majority of the craft behind our washed denim lies in Italy, but its origin — the fiber — is found on the organic cotton fields of Madhya Pradesh, India, which is one of the few places globally where long-staple organic cotton can reliably be sourced. After the cotton has been farmed it’s sent to Robecchetto Con Induno, Italy, a small commune west of Milan that hosts a 4-generation-old spinning and weaving mill that designed its renowned yarns 30 years ago and aims to become “the greenest textile company in the blue world”. This is where the organic fibers are spun into yarns, woven into a denim fabric, dyed and finished. The yarn is spun using a ring spinning technique giving the fabric the much desired artisanal character and feel. This yarn also lends itself especially well to the so-called “slasher dye” technique where yarns go through several warp beams and dye baths. It’s a method that requires less dyeing material, energy and water, especially suitable for denim styles that will eventually undergo a garment wash after sewing - like our blue and light blue jeans. Like its raw peers, our washed blue denim is cut in Urbania, Italy and sewn at its close collaborators in Monsampolo Del Tronto. Finally, the denim is washed in a facility in Grottomare, Italy with 150 years of expierence. Both our Light Blue and Mid Blue jeans are washed with Eco Stone Wash technology - only using organic enzymes, instead of stones, and significantly reducing the amount of water and energy used to achieve our charecteristic faded look and softer feel.
Beaming the yarns for our Washed Denim, Italy
Our Regular and Loose Fit black and grey wash denim are made from a midweight 13oz denim with a 3/1 structure. The Slim Fit is made from a 12 1/4oz fabric with 1% stretch for more freedom of movement. The organic cotton farmed for them is grown in Gaziantep and Sanliurfa, Türkiye, places renowned for their ideal climate and soil conditions allowing high quality cotton to grow while restricting the use of chemicals and fertilizers. After the cotton is collected, it is sent to a century-old family-owned spinning facility in the same region which — today — has turned into one of the largest textile manufacturers in Turkey. The yarns are then sent to a 300,000 sqm facility in Bursa, Turkey, for weaving and dyeing. For our Black variant, a custom developed dye is applied using reactive dyeing process on an undyed — so-called ecru — weave, penetrating everything down to the fiber to achieve a high degree of color fastness. The Grey Wash version is woven following the standard black-warp-white-weft method and is subsequently over-dyed which involves soaking the garment in a dye bath, resulting in a surface with a classic irregular pattern with white spots and a strong overtone in its overall appearance. This is all done in one of the largest denim facilities in the world and distinguishes itself by meeting both the Nordic Swan and EU Ecolabel certifications. When finished, the fabric is sent to our cutting partners in Urbania, Italy and sewn in Monsampolo Del Tronto – the same facilities that cut and sew our other denim. Like their blue counterparts, they are washed in Nereto, Italy. The Stay Black undergoes a subtle rinse with stones to soften the rigid raw denim and reduce the luster of the fabric. The Grey Wash is stone washed to achieve the faded look and even softer feel.
Dyeing the yarns for our Black Denim, Turkey
Our denim is a manifestation of what occurs when age-old knowledge meets the cutting-edge found only in the modern world. Producing world-class jeans efficiently requires a variety of skills, from those that can only be acquired through generations of research and expertise to the ability to use and manage the latest technology at high scales. The reality is that this expertise lies dispersed globally, and this can be regarded as a significant drawback from an environmental perspective. The masters of raw denim are located in Japan, the best soil conditions are in the likes of India and Turkey, and the best denim seamsters are found in Italy. At the end of the day, our primary goal is to deliver the highest possible quality product able to last as long as possible. This can only be achieved when zero compromises are made.
All our garments are co-developed with our customers. With our permanent collection we’re able to take in feedback, listen and continue to develop, evaluate and improve our garments over time, instead of constantly re-inventing the wheel.